W hy replace your cylinder when you can replace the piston for a fraction of the cost and time? Namura offers direct replacements for the original equipment as well as hi-compression and a variety of oversizes to meet your ride’s needs. They are available in 0.25mm increments, from the -1 (0.25mm) through the -8 (2mm) oversize. We also carry B (0.01mm) and C (0.02mm) oversizes which help extend the life of your expensive coated cylinders; a selection of big bore piston kits is available for some applications. Combine this with the MOS2 coating and hard anodizing, Namura gives you a higher performance piston without the higher price.
Namura piston kits come with the piston individually wrapped; a set of OEM quality rings packed in their own box, a wrist pin, and circlips.
MOS2 (Teflon/Molybdenum) Coated Skirts
A rolled-on application process provides a bond that is 10 times stronger than other spray on coatings. Benefits include increased heat transfer, reduced friction, and helping to eliminate cold seizures.
Machined Smooth Heads
Reflects combustion heat and reduces carbon buildup, protecting the top of the piston. Some tests have shown this feature can increase horsepower and fuel economy by up to 6%.
Anodized Domes
Increases heat resistance and durability; pistons with anodized domes are 75% stronger than non-anodized pistons.
Hypereutectic Casting Process
Provides higher silicon content for reduced expansion rates and additional wear resistance; it also has an ability to withstand higher cylinder temperatures.
Forged
N amura Forged pistons are engineered for high performance and durability under extreme conditions. Depending on the application, Namura utilizes advanced forged aluminum alloys—including 4032—for optimal balance between strength, thermal stability, and wear resistance. These materials allow for tighter build tolerances, excellent tensile and yield strength, and consistent performance across a wide range of operating temperatures.
SIGNATURE FEATURES
All new Forged pistons come with Namura’s signature features: 100% CNC-machine piston domes, hard anodized domes for reduced carbon build-up and heat resistance and M0S2 coated skirts for excellent break-in protection and properties.
LEADING APPLICATIONS
Also available in Top End Repair (T.E.R.) Kits that includes all gaskets, seals and needle bearings (where applicable) needed to complete an engine rebuild. From the crankcase to cylinder head, Namura T.E.R Kits include many components that most competitors don’t.
THE FUTURE IS FORGED
Hyperdryve
N amura is proud to bring you the next step in the evolution of powersport pistons. The new Hyperdryve line of pistons was specifically designed as an alternative to the OE for applications that call for the use of forged internals. The major advantage of Hyperdryve pistons is the ability to hold up under temperatures never before seen by cast pistons, without the extra cost of forged equipment.
Hyperdryve pistons are composed of a new hypereutectic aluminum alloy developed for use in the space industry. Engineered to maintain its high tensile strength up to 700°F (370°C), 50% higher than a conventional cast piston, this gives Hyperdryve the strength to perform under operating conditions normally reserved for forged pistons. Hyperdryve is the exclusive line of pistons for 250 and 450CC motocross bikes, as well as select sport quads.
Extensive testing went into our choice of material; the images below show two cast aluminum pistons that have been magnified to 1,000 nanometers. Both pistons were soaked for 100 hours at 600°F (316°C) to simulate operating conditions. It’s easy to see that the conventional aluminum alloy’s particles coarsen significantly; this weakening of the material’s bonds will lead to a sharp drop in piston strength. The particles of Namura’s new aluminum alloy have only coarsened slightly, showing that they are still able to maintain a higher strength for longer periods of time.
Figure 1
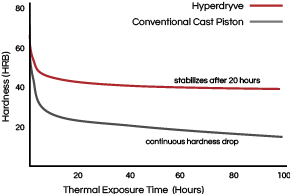
Figure 2
Material | Hardness Room Temp. (HRB Rating) |
Yield Stress 700°F (370°C) (MPa) |
Tensile Strength 700°F (370°C) (MPa) |
---|---|---|---|
Hyperdryve | 72 | 73 | 97 |
4032 Forging | 70 | 31 | 44 |
Additional testing shows figure 1 that the biggest hardness drop occurs after 10 hours of use; Namura’s new aluminum alloy still maintains twice the hardness of conventional alloys, even after 20 hours!
Still not satisfied, figure 2 illustrates the comparison of our new material to a typical 4032 forged aluminum alloy. Measurements are noted in HRB on the Rockwell scale (a hardness scale based upon the indentation impression of the material) and MPa (megapascals, a unit commonly used to measure stiffness or tensile strength of materials).
This revolutionary alloy, combined with our already existing features of machined smooth anodized heads (for better heat reflection) & MOS2 coated skirts (giving you smoother startups & break ins) meets the demands of today’s 4-stroke engines.
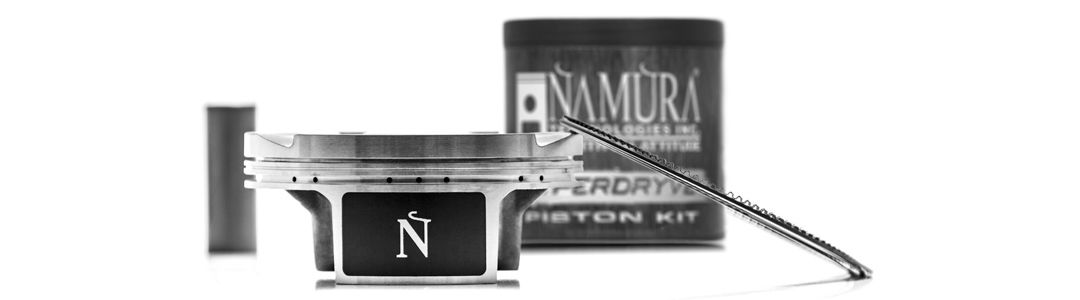
HYPERDRYVE PISTON KITS

After spending 100 hours soaking at 600˚, the particles in the conventional cast piston have coarsened and loosened significantly, leading to a sharp drop in tensile strength. The particles in the Hyperdryve piston have only coarsened slightly, displaying the strength and durability of the material. Even after 100 hours at extreme conditions, the Hyperdryve piston retains a visibly higher tensile strength.
Figure 1
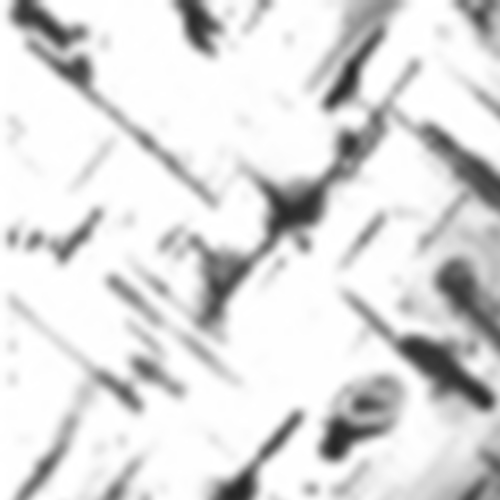
BEFORE
Before
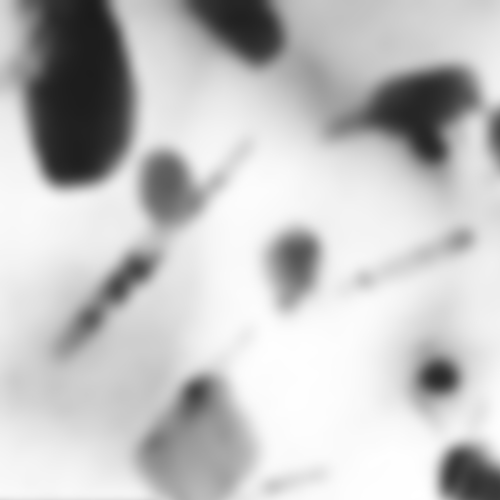
AFTER
After
Figure 2
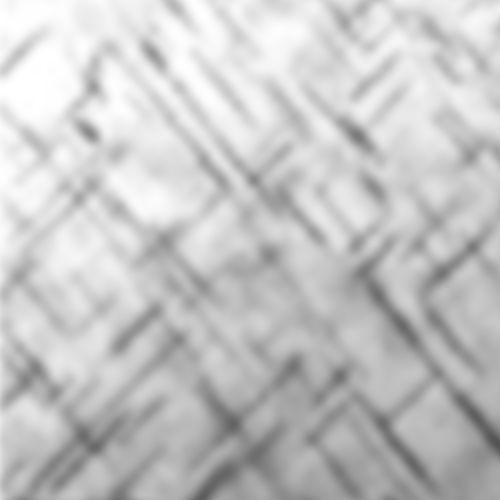
BEFORE
Before
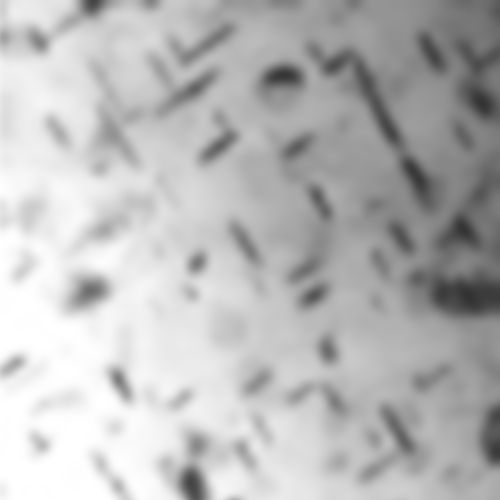
AFTER
After
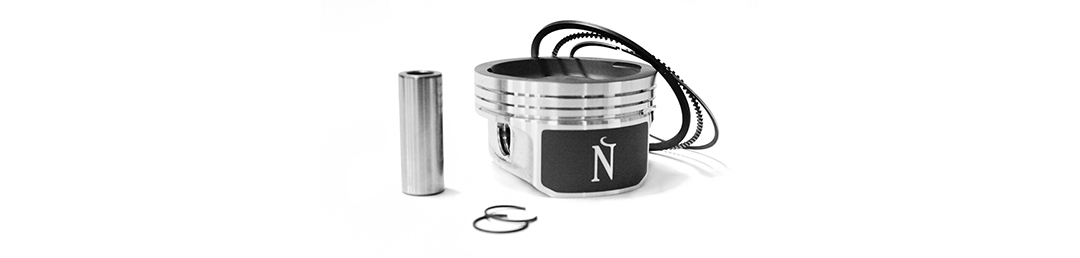